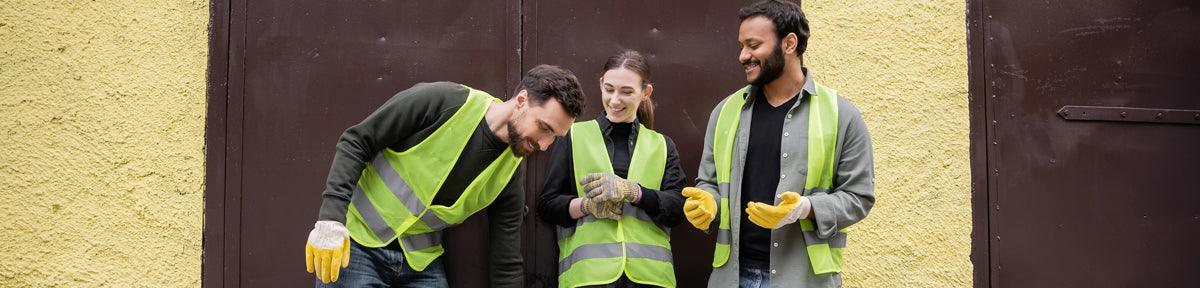
Printing on High-Visibility Garments
The majority of high visibility vests are made from polyester so they can be direct printed, heat seal transferred or embroidered, meaning they are a perfect little item to include as an add on sale. The back of a hi-vis (my name for the yellow vest that has the magical ability to prevent me getting hit by an asteroid, and if I do get struck by a rogue piece of space rock) is the easiest place to decorate with a screen print or heat seal transfer. The garments are made in lots of different places around the globe and as such they lack a consistent size area to fit a print into, always check the width between the “H” of the reflective stripes that are sewn onto the garment, the available width can change from 350mm wide on a XXL down to only 200mm on a medium. The majority of printers can all identify with the familiar complaint from the shop floor that “ this print won't fit on the mediums” after much stretching, pulling and laser precision placement the art must be modified and screens remade and production plans torn up and binned for the third time that day.
When printing onto the back of a hi-vis I would always recommend checking the classification on the garment, most are split into 3 classes that describe the amount of conspicuity that should be visible, so its never a good idea to block out all the visible area with lots of printed material.

Printing onto shiny polyester can be tricky, it hates heat, so flashing is not recommended, if you must flash then use a low power setting and a short flash time to avoid shrinkage and damage to the garment. Using higher mesh counts on multicolor designs will control the crispness of the image and allow for trouble free wet on wet printing. Progressive squeegee hardness, pressure and angle are just as important as heat management when printing multiple colors onto hi vis.
Color matching on hi-vis can be as challenging as the actual print. Plastisol works well as it has the opacity we are looking for, when printing a blue onto yellow we run the risk of the color looking too green at the end of the dryer when the base color of the hi-vis bleeds into the printed ink. This problem is especially prevalent when printing white onto hi-vis, I always try to dissuade a customer from having white in the design of a hi-vis print, black is the best color to print or navy as these give the greatest contrast against the eye-burning yellow of the safety vest.
When the customer insists that the universe as we know it will come to a crashing end if we dont have white in the design we have two options:
Migration Blocker, This ink is usually grey and has chemical blockers that will stop the putrid yellow of the innocent little vizzy crawling through the ink to turn the most optical white a lovely shade of freshly picked lemons. The ink is sticky and thick and must be printed first underneath the white and it must be flashed, already making a difficult job infinitely more complicated.
Poly White, This ink has dye blockers built in, it is usually thicker than normal white but it can be printed last so no need to flash, however the curing temp of these inks is usually lower than normal plastisol, this allows us to reduce the dryer temperature to control the point at which the polyester starts to get angry and pollute all the bright colors in proximity. Be careful to also use low cure colors in the rest of the print to avoid a mis cure on the other parts of the design.
Curing the ink on hi-vis can be a challenge as the reflective strips are usually sewn with a brand of thread that can only be purchased in the back streets of an undisclosed location, as it has the unique magical ability of shrinking to approximately a third of its length when a pre designated heat is reached, it never reacts at the same temperature twice and it pulls the garment in different directions according to the position of the stars on that particular day !! this means we must find the sweet spot of curing temperature and speed that allows the ink to stick to the garment but not pucker the reflective strips so they resemble an instagram influencers top lip!
Hi Visibility garments are not limited to vests and we now see a wide range of garments ranging from jackets that have a handy zipped print access to allow us to print onto the outer ply only, to trousers that can be transferred using a sleeve board, but we also have the ability to print the reflective ink onto a shirt to give it hi visibility qualities, it is important to note the HSE classification of what makes a garment a Hi Vis garment, Reflective ink has changed over the years, I can still recall over 25 years ago using the 3M product that was very expensive and consisted of a three pack of binder, shiny reflective cats eye glass balls and catalyst. This ink was difficult to use, it clogged in the mesh and had a short shelf life and to be honest it did not sit very well onto textiles. Now the new ranges of ink available have all these properties built in and have a long shelf life, I recently printed some fluorescent yellow long sleeve shirts with a water-based ink that was very stable and gave superior reflective properties when printed through a 55t mesh. They were used in a motorsport pitlane and I must stress they do not conform to the EN 471 standard of normal hi-vis vests but they looked super cool! Plastisol reflective ink is also available as a single pack ready to use ink.
Branded Hi-vis are now a staple product in most print shops and the option to heat seal is usually the first one we pick due to the low quantity print runs but it is possible to print a single color job of 30 pieces inside 15 minutes using screen printing, making it a viable decoration option.
Article written by Tony Palmer, Palmprint
Tony has more than 30 years experience in garment decoration ranging from manual screen printing on hand carousels to the operation of multi-color automatic presses. Specifically Tony is an expert on MHM Automatics, Tesoma, Exile Spyder, Douthitt CTS, Zentner, and numerous manufacturers of textile decorating equipment.
#spsiinc #palmprint #mhmscreenprinting